Varnishes
Paper varnishes applied to paper stock give a smooth and consistent texture to the page. Varnishes seal the printed material to help preserve it, and are glossy, dull, or matte. They can even be tinted.
Varnish can be flooded across an entire printing surface. It creates robust paper stock, without adding too much weight. This makes is suitable for magazine pages and covers, brochures, and coffee table books.
It can also be spot applied precisely where it’s required.
Spot UV Varnishes
Spot UV varnishes are applied to the printing surface and cured, or hardened, during the printing process by exposure to high-intensity ultraviolet (UV) light. This creates a high-gloss coating on the surface of your print. UV varnishes are typically used as spot applications. Spot applications are specific parts of a page that are varnished, while the rest of the page remains untreated.
Spot UV varnishes are ideal for adding texture and character to printed surfaces, highlighting key elements of your design and enhancing colours.
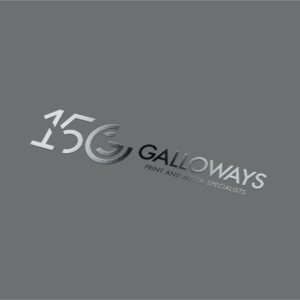
Lamination
The process of laminating adds a layer of protective coating (usually some type of plastic) to the printing surface. Glossy or matte, lamination improves paper stock sturdiness and water resistance. Lamination also lends a sleek and smooth finish to the printed surface. High gloss lamination makes photos and images appear to have greater contrast and enhanced sharpness. Matte laminated prints are more subdued, offering an elegant, luxury finish to the printed product.
We recommend using lamination for high-contact print items, such as business cards, soft-covered brochures and books.
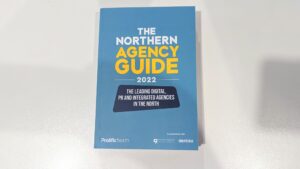
Foil Stamping
Foil stamping, also known as hot foil stamping or foil printing, is a printing technique that doesn’t use ink. Instead, foil is applied to another material to achieve a desired finish. Similar to embossing or debossing, foil stamping applies both heat and pressure to create unique printed designs. It creates reflective elements to your design, and suggest luxury.
Foil stamping can be applied to most paper stocks, although it works better on uncoated and stock shouldn’t be too thin or porous. Foil stamping offers a choice of different metallic finishes and a broad spectrum of colours, including gold, silver, pigmented, and holographic. Logos, accents, and borders – all look great when they’ve been stamped with foil.
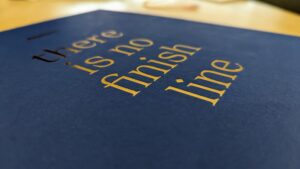
Embossing
The term embossing refers generally to a process that raises parts of a page for subtle emphasis and texture. Consumers literally feel the result, making their handling experience interesting.
The substrate material (paper, or cardboard for example) is pressed into a female die with a design etched into it. Underneath the substrate is a male version of the same design. The two dies are pushed together under pressure and heat. The result is that the design is embossed into the substrate, adding a tactile dimension to your design.
Embossing can also be combined with other printing techniques such as foil stamping to enhance the effects of both techniques. Embossing leaves a mirrored indentation on the reverse side of the substrate material.
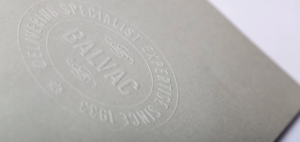
Letterpress/debossing
Letterpress printing is one of the oldest printing techniques known, dating back to the early 15th Century. Some printers use the term debossing. This process is used to depress or indent certain portions of the page and gives a vintage effect.
Traditionally, the letterpress printing technique was used only to apply ink on a page as a form of relief printing and then usually only for text. But it has evolved to also include pressing logos and other design elements directly into the paper substrate.
For debossing, the substrate is simply turned upside down to the and pushed below the surface. If the stock is thick enough, there will not be an imprint on the reverse side of the paper.
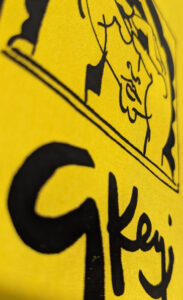
Die Cutting
Die cutting works in much the same way as a cookie cutter. Metal shapes, called dies, punch, cut, form, and shear paper into the shape and size required. It’s a highly skilled discipline, that is used across many industries.
The origin of the phrase comes from the 1300s, and the middle English word “de”, meaning put or placed, when dies were predominantly used to stamp or cast metal coins. In the 1800s, the term die cutting meant a method for cutting leather soles instead of by hand, creating more precise and accurate shoe sizes.
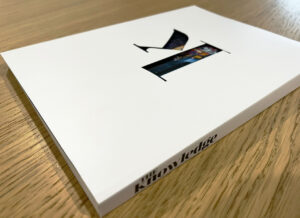